CNC simulation is an extremely valuable resource because it has the power to plan and verify CNC machining. It includes all the components found in the CAD CAM software environment. In other words, you can “predict the future” of your machining and optimise time, processes and resources.
This technology stores all machines, accessories and clamping systems, precisely and on time in the virtual production environment. The simulation creates digital copies together with all components.
With the output from the CNC simulation, the process becomes not only safer, but also more effective and efficient. This is because this technology is able to detect possible collisions or more general problems that may arise during the machining.
All common CNC machines, such as complex multi-axis machines, lathes with live tooling, multitasking machines such as turning-milling units, deep drilling tools and anthropomorphic robots with additional axes, lend themselves perfectly to this type of simulation.
The optimisation of CNC programs provides a variety of options to be chosen and defined each time according to the machining conditions. For example, you can change the machine, the tools or the machine head, change the setup settings, adapt the rotation of the axes or even the orientation of the head.
The potential of CNC simulation
Let’s take the example of the Vericut simulation software proposed by the Californian software house CGTech.
One of its special features is the ability to virtually recreate the working environment of a real machine tool.
Within this software, in fact, it is possible to:
- import the geometric models to establish the overall dimensions to be checked;
- define the kinematics of the machine;
- load the numerical control emulation;
- implement all the customisations relating to the individual machine tool, such as variables, sub-programs, macros and M-codes.
It must be considered that the virtual machine used in everyday life to perform operations such as machining with chip removal is equipped exactly like the real one. This technology sets up the clamping elements, the various tools, the blank, the post-processed work programs and immediately executes the complete work cycle.
In addition, the CNC simulation allows you to understand how much time will be needed to develop the machining and plan the steps in the best possible way. Production will benefit because the machining times on the CNC machine will be calculated automatically.
Error reporting and monitoring of time variation of quantities
CNC simulation, achieved through the continuous changes and improvements of the digital transformation in Industry 4.0, is essential for receiving error reports during machine operation.
In fact, during the simulation, machining movements are identified. Through a dedicated window, problems of end-of-stroke, collisions, syntax inaccuracies, etc. are brought to light. This is also possible thanks to the way in which the machine can be stopped at any time during the CNC simulation, in order to check feeds and check the model obtained.
The ability to stop the simulation at the precise error point allows the software user to become familiar with the virtual working environment. In this way he can realise the advantages of this approach and feel more secure when he actually moves on the real machine.
In other words, CNC simulation helps to obtain digital twins that faithfully reproduce all the components of any production environment in real digital libraries.
In addition to the considerable benefits in terms of error control and process correction, CNC simulation maximises the return on investment of the entire workshop.
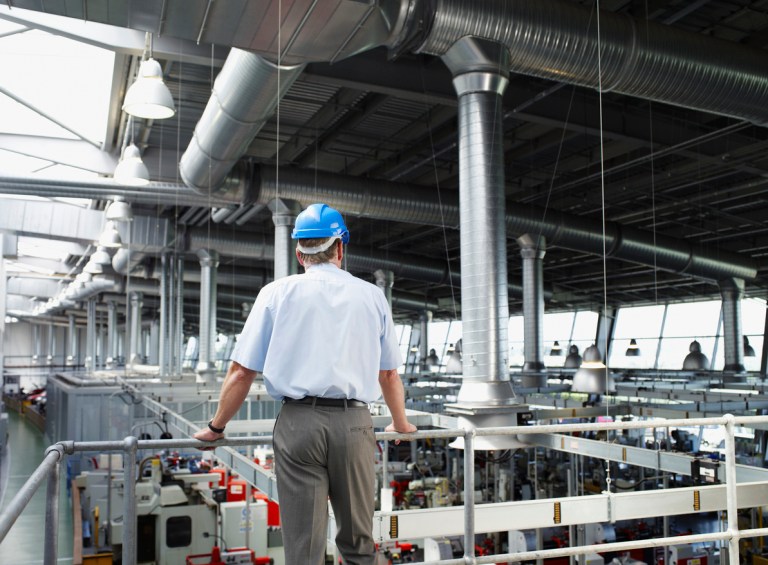
The operator has a lot of information at his disposal about the configuration of the working piece, the component and the tools. And as mentioned before, when a machining operation suddenly requires an improvement, it is possible to intervene in real time.
Not to be underestimated, then, the possibility of checking the tool paths several times through the integrated postprocessors.
By comparing the machined output with the original model, the result is that each machined part is perfectly identical to the designed model.