No sector has been spared by the digital transformation. All of them, in one way or another, have been affected by digitization and automation processes that have improved productivity, cut unproductive steps and much more.
Even the pharmaceutical sector, despite its high level of regulation, has undergone digital transformation processes that have affected not only production, but also quality control and the integrity of scientific data.
Thanks to this technological evolution the sector is moving ever faster towards what has been defined as Pharma 4.0. In other words, a new organizational and production paradigm that does not only involve the plant itself, but involves all the players in the pharmaceutical sector, from the research laboratories to the distribution system.
What is Pharma 4.0
Pharma 4.0 (from the International Society for Pharmaceutical Engineering) refers to the framework for adopting (and adapting) digitization strategies within the unique context of pharmaceutical manufacturing. In few words, Pharma 4.0 translates into greater use of connectivity within the manufacturing plant and across the pharmaceutical company’s sites; an increase in the level of productivity; easier and faster compliance with new state and supra-state regulatory requirements; and the ability to respond quickly to problems as they arise.
As mentioned above, what Pharma 4.0 brings to the pharmaceutical sector does not only concern the production sector, but also research, development and distribution sectors. A holistic approach, therefore, which makes extensive use of tools such as big data, artificial intelligence algorithms, collaborative robotics and distributed cloud-based architectures. In this scenario, communication systems play a key role, allowing information to be distributed both inside the plant (to the robots used in the production process, for example) and outside (to suppliers or logistics departments).
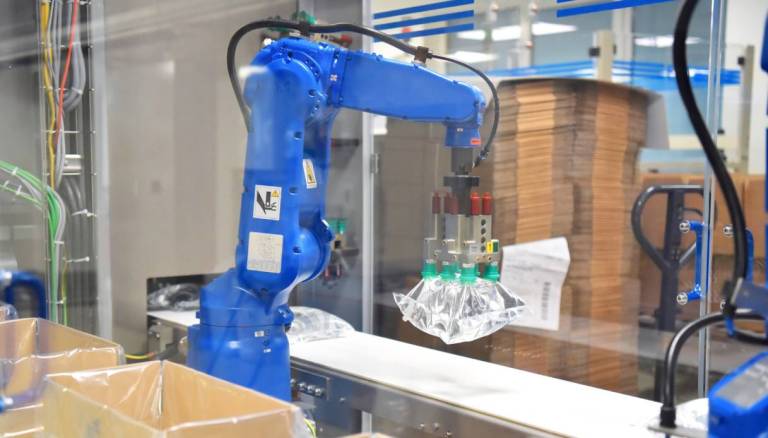
How to implement a digital transformation program in the pharmaceutical sector
For a pharmaceutical company which intends to transform itself into a “Pharma 4.0” reality, it is necessary to undertake a rather long path, divided into two “macro-phases” including several steps. In the first of the two phases, the “as it is” state of the company will be studied: first of all, the management identifies the priority objectives that the company intends to pursue through the transformation; it will then move on to the analysis of the technological infrastructure and the cloud tools available; it will study the “conformation” of the production site and its possible inefficiencies (or shortcomings) on which to intervene; finally, the skills of employees and managers will be assessed to identify any gaps to be covered with new hires.
The second phase, on the other hand, is the operational phase, during which the information initially collected will be put into a system to start the digital transformation and thus obtain all the advantages guaranteed by the Pharma 4.0 paradigm. Management and staff will first scout the market for the most suitable technological solutions for the company’s needs, then carry out a pilot project to assess the effects of implementation on a small scale, and finally proceed with the full roll-out of all solutions.
The impact of Pharma 4.0 on pharmaceutical production
Pharma 4.0, as thought by the International Society for Pharmaceutical Engineering, is a holistic process, involving every single aspect of the pharmaceutical industry. If you think that everything is solved by only using robots in the factory and the consequent automation of the production of medicines and the packaging process, you could not be more wrong. This is just one of the many effects that the digitization and automation process brings to the production site.
At the heart of the transformation is big data – the myriad of data that pharmaceutical companies can obtain both internally (from laboratories, production sites and distribution infrastructure) and externally (from other research organizations, for example). By using this information and putting it into a system, it is possible to make business more efficient at all stages. Data analysis, for example, makes it possible to speed up the procurement of raw materials, the production process and quality control. In addition, it is possible to monitor the distribution chain and have continuous feedback from the patients to whom the drugs are administered.
The adoption of the new production/organization paradigm also allows the pharmaceutical company to adapt more quickly to any new requirements or requests from organizations and regulatory agencies in the sector. The use of new technologies, in fact, makes it possible to raise safety standards both in the production phase and in the packaging and distribution phase.